Because there are several bushing kit options marketed, we field this question often, “Which bushing kit is the best fit for me, and why?” Of course, we should factor time (of the repair/job and maintenance), price and quality. Exapta delivers quality—with every product. There are three main, but different, characteristics to consider if you are looking for quality: steel, nylon and teflon.
Before making your selection, let us breakdown the differences. The decision is yours.
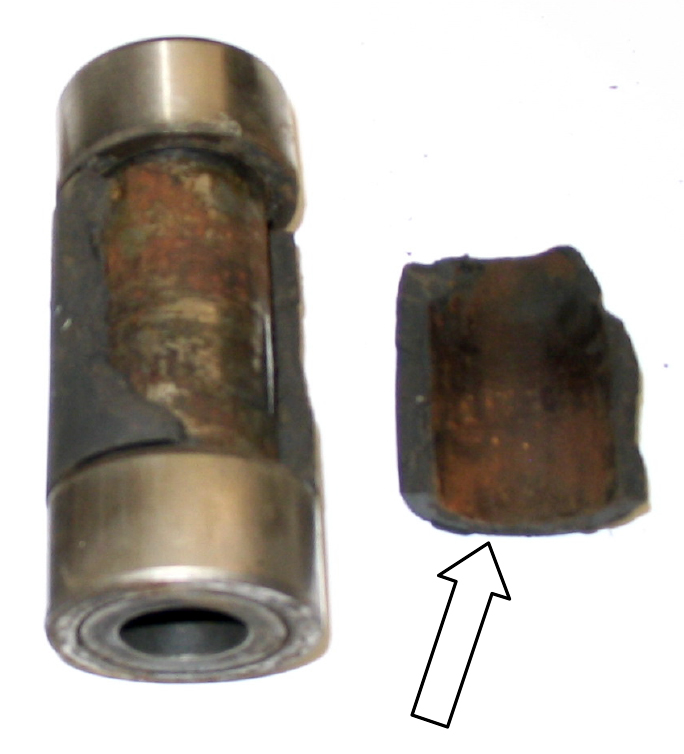
Steel
OEM and some aftermarket suppliers use steel bushings. Why? Steel is strong and steel is less expensive. What’s wrong with steel? Steel needs grease (there’s that time factor) for lubrication to slow the wear from the friction of steel on steel. In a dirty, dusty environment, the grease and dirt pack together, becoming rock-hard. Many times, this dirt/grease combination becomes so tight you cannot get these pivot points to take grease. This is the primary reason closing and firming arms seize and lock up. Some farmers (very few) even choose not to grease because of this problem —resulting in excessive wear of all components at the pivot point.
Nylon
There is a nylon bushing kit on the market. The upside to nylon versus steel is that it has lubrication properties so it can be considered “greaseless” which gives it an advantage over steel. But beware, nylon lacks the load carrying capacity and shock resistance of steel and Teflon. The issue is that nylon is actually quite soft and not so durable in this application. Nylon bushings do not withstand the harder angular hitting force from the side-to-side movement of the arm, causing them to shift inward/together (which they already slide in easily from the get-go). If the bushings move inward/together, this creates space towards the outer edges, causing the bolt to rock—increasing bushing wear. This results in the joint loosening, causing the bolt to bend and again, intensifying wear. Bushing shift is a hidden problem that is not obvious unless you are looking for it, but can cause real issues like more side-to-side movement and excessive wear. Last, but not least—nylon is prone to absorb water which leads to swelling and component seizure of the bushings.
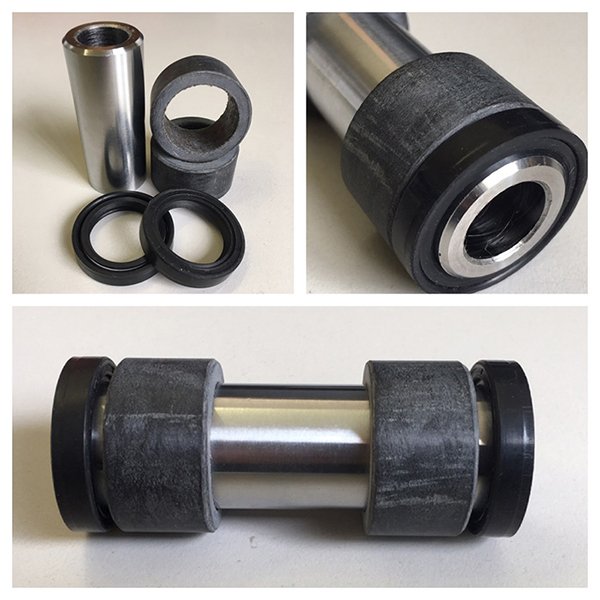
Teflon
Teflon is the superior “greaseless” bushing with higher load carrying capacity and better shock resistance than nylon. How? The bushings are fiber-wound Teflon infused. Teflon, with its own self-lubricating properties, does not require grease like steel (thus avoiding the problem of the rock-hard dirt/grease combination) and provides much lower coefficients of friction than nylon. The Teflon bushings are “tough” like steel, versus the nylon bushing that can literally be imprinted by a fingernail. Unlike nylon bushings, Teflon provides excellent contamination and wear resistance and does not absorb water the way Nylon does. The Aricks Bushings with teflon seals, are the truly greaseless solution with exceptional wear resistance that will save you time and frustration when servicing your drill.
Aricks Bushing Kits with Teflon meet Exapta’s product line-up criteria, which is to provide top-shelf products that outperform and last longer than any other solution on the market.