Many of you know that I view these drills as being superior to many others on the market because of: 1) depth gauging alongside the blade, 2) an in-furrow seed-lock wheel. Yet there are plenty of shortcomings with these drills, and Exapta has been busy addressing those.
Perhaps the worst downfall of these drills is the way that down-force is applied to the opener—the rockshaft twists to compress a big coil spring on each opener. Some will say that the swing-arm design, where the opener pivots from a single point (rather than a parallel link) is the worst downfall. While it’s true that a swing-arm isn’t as good as a parallel link, the worst issue with the 50/60/90 opener is actually the way that down-pressure is applied to it. Because the spring is nearly parallel to the swing-arm, it has almost no down-stroke—i.e., the spring is in the optimum position (applying the correct amount of downforce) for only about 0.25-inch of its range. Had the spring been oriented in another direction (e.g., pushing straight down), the problem wouldn’t be nearly so bad.
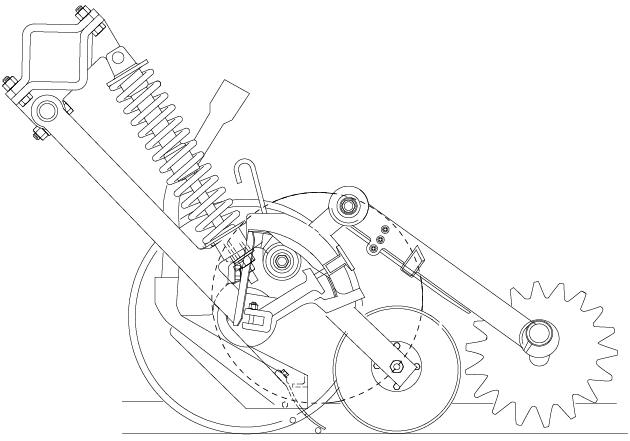
But as it stands, you must have fields that are laser level for the openers to work correctly. Even 0.5-inch depressions give them fits. The spring starts to relax as the opener goes into these miniscule depressions, and you lose downforce—the opener loses depth, and starts hairpinning. To compensate, everyone cranks the pressure way up—so that the majority of the openers have far too much pressure, just to keep those passing thru mild depressions working halfway decent. You end up with excessive sidewall compaction on most of the rows, while some aren’t even holding depth.
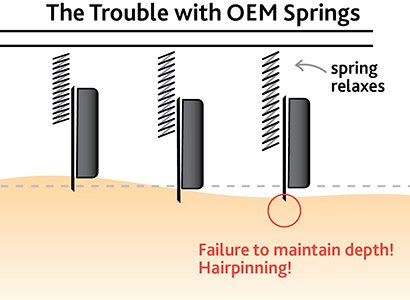
We set about to fix this design hiccup, and chose hydraulics to do it–what we call our UniForce system. Now, we get uniform pressure on every single opener throughout its full stroke. The result is much better cutting, less hairpinning, holding depth much more accurately, and far less sidewall compaction. Another problem with springs is that they bounce–so the opener hits a hard spot, or a rock, and it bounces. Hydraulics don’t have this problem. When developing the UniForce, we’d often leave at least one opener with the OEM spring. Watching them run side by side, it’s amazing how much the row(s) with OEM springs bounce, whereas the rows with UniForce are smooth and steady.
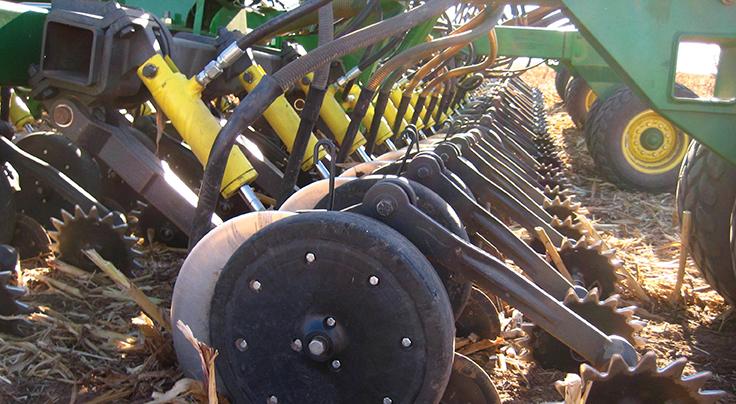
UniForce uses a single-action cylinder along with the OEM rockshaft, which is still used to raise and lower the openers. A sequencing valve (built into our custom valve block) switches between the two circuits.
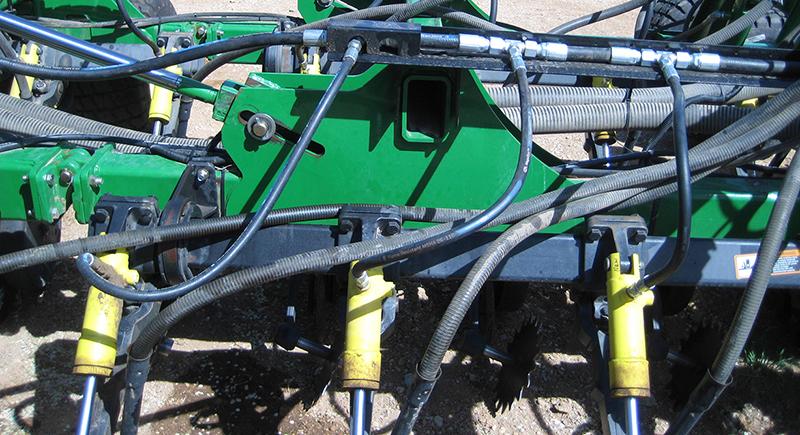
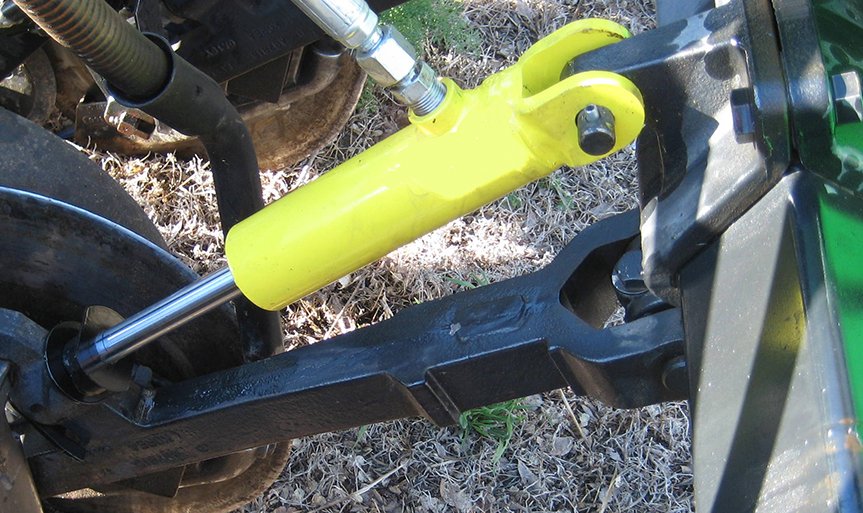
The UniForce single-action cylinders a re an easy swap-out for the OEM springs. (Assembling all the hydraulic hoses takes a bit longer.)
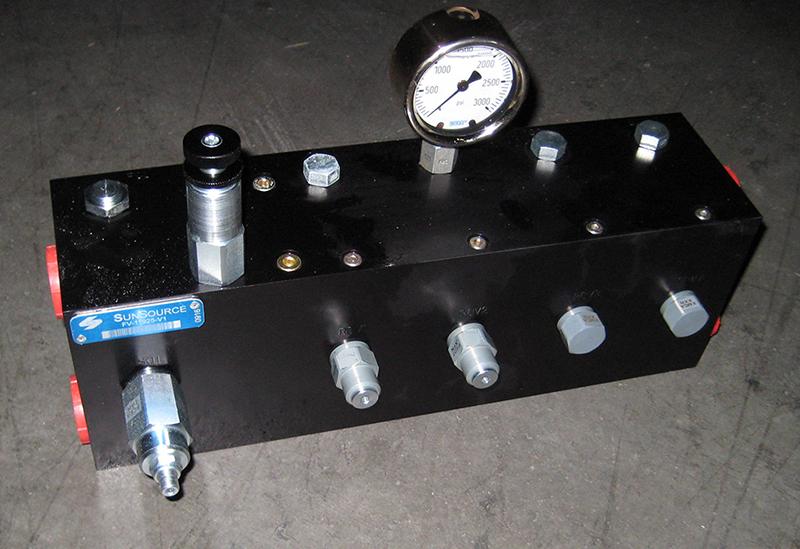
An in-cab control is also available as optional equipment and can be added at any time. It allows changes of pressure on the openers while on the go.
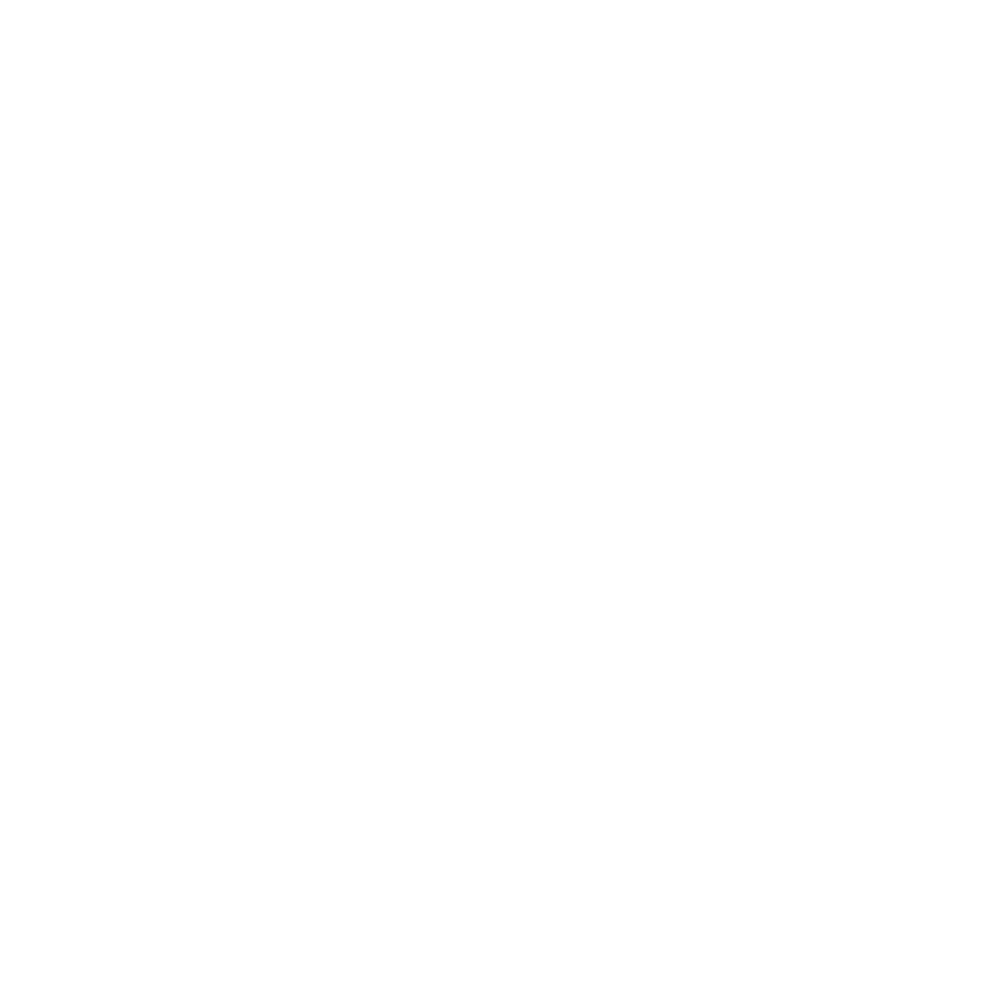