By Levi Metzger
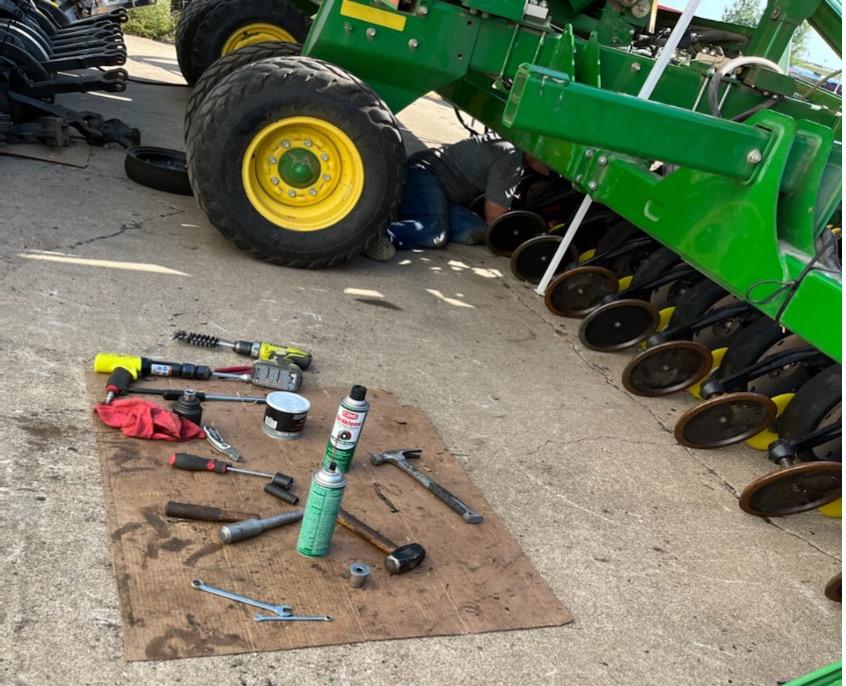
When looking at things that need to be upgraded on your operation, perhaps your air seeder comes to mind. Maybe the newer N series drills from John Deere have caught your interest. John Deere has made improvements over the 90 series in areas such as the closing and firming wheel. They have also narrowed the profile of the seed boot. While Deere has changed things a bit, Exapta has been offering modifications to take care of these issues for years.
At Exapta, we are confident that a 60 or 90 series John Deere air seeder or box drill can be completely rebuilt and perform better than a new John Deere N series drill coming out of the factory. Settling for a low trade in value on your existing drill is likely not your best option. This is no secret to most folks who have experience with these drills, but in this newsletter, we will dive deep into the numbers to answer the question that many might be wondering: Just how much money can I save by rebuilding a drill?
In my discussions with farmers, I generally feel that there are two roads to take with air seeders. Either you have a newer and well maintained drill that you trade often, or you keep rebuilding an existing air seeder. Once you commit to one of these avenues it seems like it is best to stay on it. It seems like lately, trading for new is more attractive than usual due to the used equipment market being higher. If you are pleased with the trade in offer the dealer gives you, the N series does offer some nice features including increased air cart capacities, and better clearance on CCS drills for accessing row units under the seed tanks. However, if you don’t feel that you are running the drill over enough acres every year to justify a new machine, rebuilding as needed is usually the more attractive option.
My goal was to look at the cost of every available size of N series air seeder and 1590 box drill set up on 7.5” row spacing from John Deere and compare what it would cost to completely rebuild a similar 60 or 90 series drill. I did not include CCS drills, 1895’s, 50 & 60 foot drills, or 10” spacing drills, but all the concepts would still apply to those models. When considering a total rebuild, I am including every wearable piece of the opener on the tool bar and all of the air delivery system on the drill including hoses up to the meter housing on the air cart.
I have determined the exact cost to rebuild one opener of a 60 or 90 series drill with Exapta products, which is reflected in Table 1 below. I then used this number along with other data to determine the exact parts needed to update the air system and came up with an exact rebuilding cost for each of the drills listed in Table 2 below. This table also compares rebuilding costs for existing machines to the prices listed for new air seeders and box drills on Deere’s website. All prices in the furthest right column include 4.5” spoked gauge wheels and spiked closing wheels as options from Deere.
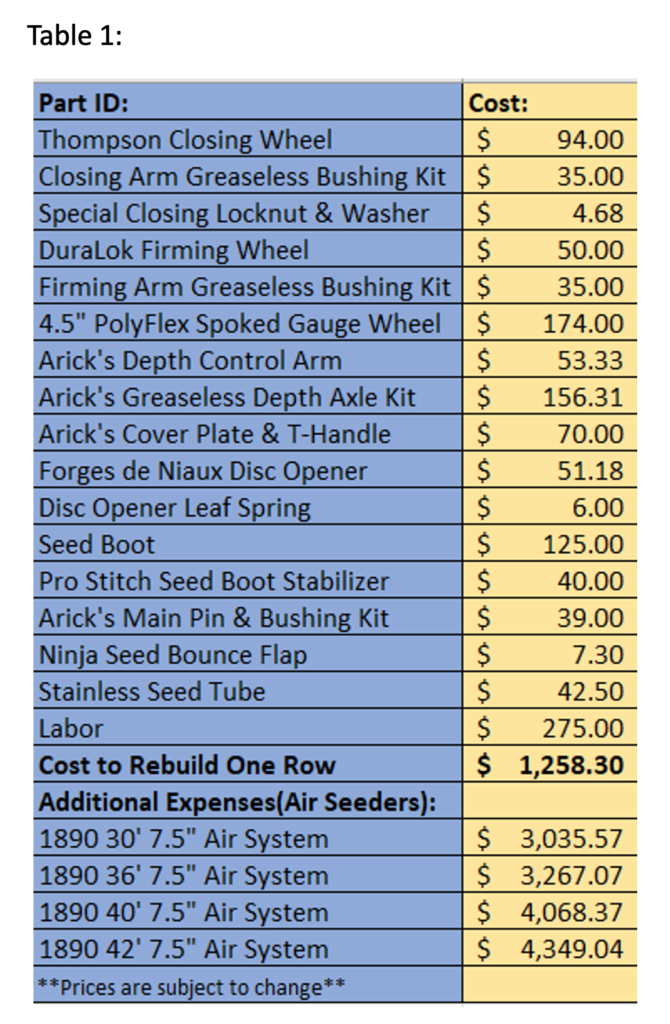
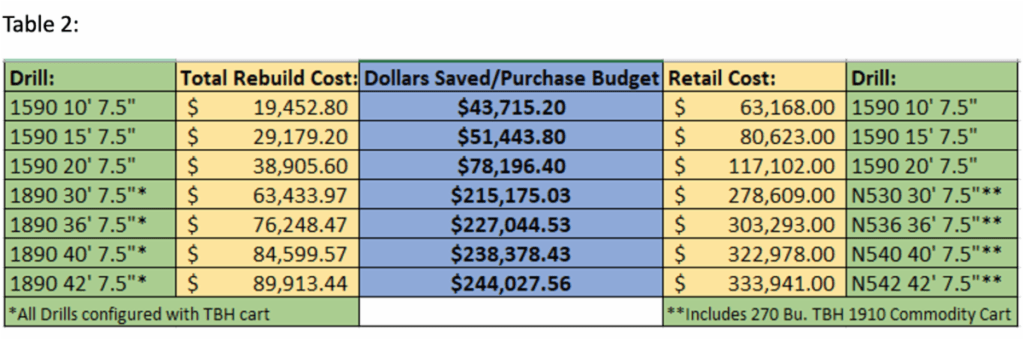
As you can see some serious savings can be realized when it comes to rebuilding drills. Keep in mind that the prices on the right column for new drills are all set up with the smallest 270 bushel 1910 commodity cart available from Deere, which is priced at $109,995. The most expensive 1910 comes in at $223,824. If you can find a good rebuilder or are up to the challenge yourself, it can be a very good investment for your operation. Not only is this a good tool for finding how many dollars you kept in your pocket, it is helpful in determining what to pay for a used drill that might need a lot of work or what your current drill’s value might be. This is also assuming a drill is totally shot and needs everything replaced right away which is not often the case. You could slowly rebuild the drill and incrementally improve it year to year. By doing this you can pay to improve an existing air seeder instead of paying interest on a loan for your new drill that will likely need more money put into it once you are done paying it off.
I recently saw a 40’ 1890 with the air cart sell on auction for less than $25,000 and it was not completely shot. I figured that particular farmer saved himself at least $200,000. That leaves him a lot of room in his budget for extras like new tires and hydraulic hoses, stainless meter housing on the air cart, an Intelligent Ag Blockage System, or a UniForce Hydraulic Down-pressure system, all of which would take seeding performance to the next level.
Exapta is ready to help meet your goals in drill performance. Call us today at 785-820-8000 to discuss how we can make your box drill or air seeder literally perform better than new, or to chat about the content in this newsletter.